1. Comprehensive Quality Control Philosophy
1.1 Rigorous Incoming Material Inspection
- Automated Cell Sorting and Testing:
Every incoming cell is automatically sorted and tested using a state-of-the-art automated system. Key performance parameters are matched to strict tolerances:- Voltage Variance: ≤0.005V
- Internal Resistance Variance: ≤0.5Ω
This precise screening ensures that only cells with nearly identical performance enter production, laying a solid foundation for consistent battery pack performance.
1.2 High-End Materials and Structural Protection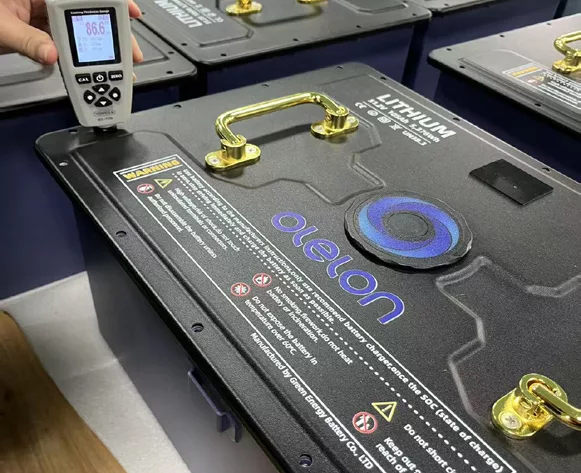
- Heavy-Duty SPCC Casing with Duplex Corrosion Protection:
The battery casing is fabricated from heavy-duty SPCC steel that receives a 20μm electrophoretic coating followed by a 60μm paint layer. This duplex protection provides exceptional corrosion resistance.
- 9-Point Random Thickness Testing:
The casing (including internal components) is randomly tested at nine points to ensure a minimum thickness of ≥80μm, exceeding the capabilities of economy-grade competitor treatments.
- 9-Point Random Thickness Testing:
- 800 Hours Salt Spray Testing:
The battery is subjected to a rigorous salt spray test (5% NaCl, 80kPa spray pressure, for 800 hours), which is equivalent to 10 years of coastal exposure. This high-precision engineering certifies that the battery can perform reliably even in harsh coastal conditions.
2. Battery Testing Procedures
2.1 Charge Testing
- Standard Charge Process Evaluation:
The battery is charged under controlled conditions (constant current/constant voltage phases) to confirm the accuracy of the charge cutoff. This process is repeated over many charge–discharge cycles to ensure consistent performance and safety. - Overcharge Safety Testing:
Overcharge tests are conducted to verify that—even if the charging conditions exceed the design specifications—the battery’s built-in protection mechanisms (such as thermal cutoff and voltage regulation) prevent overheating, swelling, or ignition.
2.2 Cell Testing
- Capacity and Internal Resistance Measurement:
Each individual cell undergoes high-precision testing to verify its true capacity and to measure both DC and AC internal resistance. This guarantees that the performance of every cell meets design specifications. - Uniformity Check:
An advanced automated testing system simultaneously evaluates multiple cells, ensuring consistency in capacity, resistance, and overall performance. This uniformity is critical when assembling multiple cells into a battery pack.
2.3 High/Low Temperature Testing
- Environmental Simulation:
Batteries are cycled through extreme temperatures (e.g., high temperatures up to 50–60°C and low temperatures down to -40°C or lower) to simulate the operational challenges encountered in harsh climates. - Performance and Safety Evaluation:
During these tests, key parameters such as charge/discharge efficiency, capacity retention, and internal resistance are monitored. Additionally, the tests check for any leakage, swelling, or short circuits under temperature stress. - Temperature Equilibration:
Prior to testing, the battery is allowed to reach thermal equilibrium at the set temperature to ensure that measurements are accurate and representative.
2.4 Vibration, Impact, and Pressure Testing
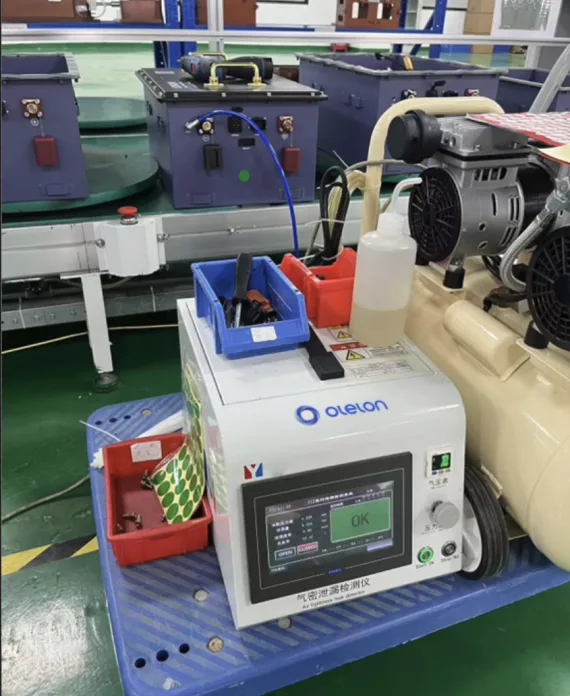
- Vibration and Impact Tests:
The batteries are mounted securely and subjected to sinusoidal vibration and shock tests that simulate conditions during transportation and real-world usage. This ensures that the battery’s structure remains intact and that no components become loose. - External Short Circuit and Crush Tests:
Batteries are challenged with external short-circuit conditions and crushing forces to validate the performance of safety features, ensuring that the battery remains sealed and structurally sound even under extreme stress. - Air-Tightness Testing:
Using an air leak detector with pressure testing, the battery is confirmed to have complete gas tightness, effectively managing internal pressure through a well-designed vent (VENT) system.
2.5 BMS Installation Pre-Check
- 3-Stage Rigorous Inspection Process:
Prior to the installation of the Battery Management System (BMS), every battery undergoes:- Visual Inspection:
A meticulous external check to identify any visible defects. - Thermal Shock Testing:
Rapid temperature changes are applied to evaluate the resilience of the battery and its components. - Functional Circuit Test (FCT):
In-depth electrical testing of the battery’s circuitry to ensure proper functionality of protection and monitoring systems. This three-step inspection ensures that each battery is fully compatible with the BMS and ready for final assembly.
- Visual Inspection:
2.6 Advanced Laser-Welded Technology
- High-Precision Laser Welding:
The assembly process employs state-of-the-art laser welding technology with a tolerance of ≤0.05. This results in robust, precisely aligned joints, elevating the battery’s construction quality to near-art levels and ensuring that every weld passes stringent mechanical and safety tests.
3. Packaging and Shipping
- Standard Wooden Crate Packaging:
Batteries are packaged in standard wooden crates designed to protect the product during transit. - Compliance with UN3480 and Class 9 Regulations:
The packaging meets all international hazardous material transportation standards, ensuring safe transit and adherence to UN3480 regulations for dangerous goods.
4. Summary of Key Advantages
By applying a comprehensive series of rigorous tests and quality control measures—from incoming material inspection, automated cell sorting, high-precision charge/discharge testing, and extreme temperature cycling to vibration/impact testing and airtightness verification—Olelon achieves the following:
- Exceptional Consistency and Stability:
All incoming cells are precisely matched in voltage (≤0.005V variance) and internal resistance (≤0.5Ω variance), ensuring that each battery pack exhibits uniform performance. - Outstanding Environmental Resilience:
Through extensive salt spray (800 hours) and high/low temperature testing, Olelon batteries are confirmed to operate reliably even in corrosive coastal environments. - Complete Safety Assurance:
A comprehensive suite of tests—including overcharge, external short, vibration, impact, and air-tightness assessments—ensures that batteries can withstand unexpected conditions and remain safe under all circumstances. - International Compliance:
From BMS pre-checks and advanced laser welding to UN3480-compliant packaging, every process stage adheres to the highest international standards for quality and hazardous material handling.
By implementing these rigorous testing protocols and high-end production techniques, Olelon demonstrates its commitment to producing batteries that not only meet but exceed market expectations in terms of performance, safety, and reliability. This comprehensive quality assurance process is designed to instill confidence among dealers and end-users alike, ensuring that every Olelon battery delivered is a symbol of engineering excellence and robust design.